Tackling Information Silos Problems in Farming Equipment Repair
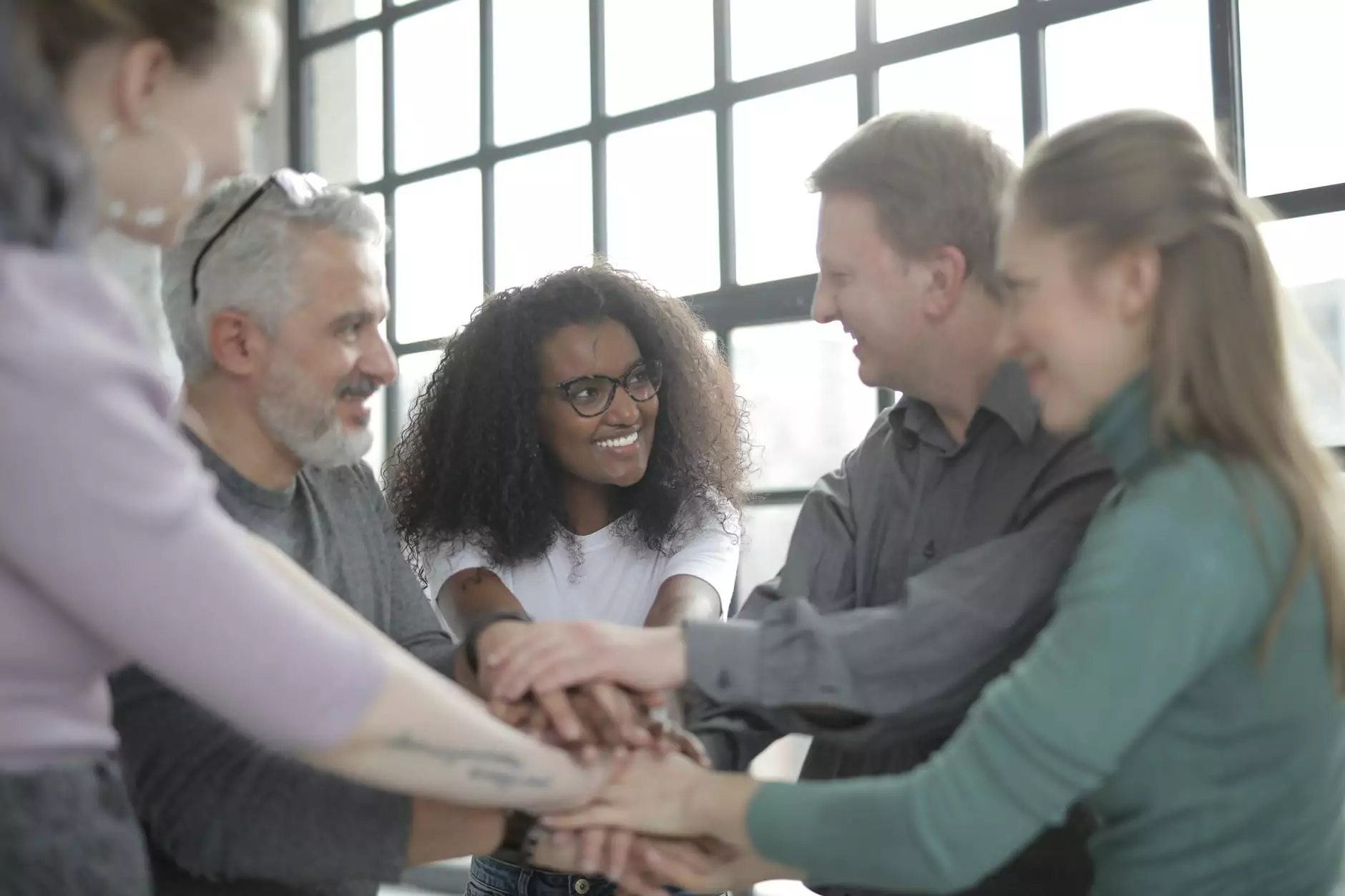
In today's rapidly evolving business landscape, information silos problems pose significant challenges, particularly in industries such as farming equipment repair. Understanding what these silos are and their impacts can equip businesses to innovate and thrive in a competitive environment. In this comprehensive article, we will delve into the essence of information silos, explore their ramifications within the farming sector, and provide actionable strategies to dismantle these barriers.
What Are Information Silos?
Information silos refer to the phenomenon wherein data, resources, and knowledge are isolated within specific departments or teams of an organization, preventing seamless communication and collaboration. Often characterized by a lack of shared information and uncoordinated organizational efforts, these silos can stymie productivity, hinder decision-making, and undermine overall operational efficiency.
The Impact of Information Silos in Farm Equipment Repair
In the context of the farm equipment repair industry, information silos can have dire effects:
- Decreased Efficiency: Without a centralized database, field technicians may struggle to access crucial repair histories or component specifications, leading to delays.
- Inconsistent Communication: When departments do not share information, repairs relevant to specific machinery can be overlooked or mismanaged.
- Inability to Leverage Data: Valuable insights from customer feedback or equipment performance metrics often get trapped within departments.
- Impacts on Customer Satisfaction: Slow response times and lack of coherent service can frustrate clients, leading to diminished trust and potential loss of business.
Recognizing the Symptoms of Information Silos
Identifying information silos is the first step toward resolution. Here are some telltale signs your farming business might be suffering from this issue:
- Frequent Miscommunication: Teams frequently misinterpret or lack information about processes or repairs.
- Data Duplication: Multiple teams record the same data differently, leading to inconsistencies and confusion.
- Slow Project Completion Rates: Increased time to complete repairs due to the lack of collaborative tools or data availability.
- Frustrated Employees: Staff expressing dissatisfaction with workflows due to blocked communication channels.
Strategies to Break Down Information Silos
Implementing effective strategies can help mitigate information silos problems in your farm equipment repair business:
1. Foster a Culture of Open Communication
Encourage cross-departmental communication by initiating regular meetings or collaborative projects that require input from various teams. Emphasizing teamwork can create a shared sense of purpose and dissolve barriers.
2. Implement Collaborative Tools
Adopt technology solutions such as cloud-based project management and communication tools. Platforms that enable real-time sharing and collaboration can dramatically reduce the risk of information silos.
3. Centralize Your Data
Establishing a centralized database where all teams can access pertinent information regarding machinery, clients, and repairs can ensure that everyone is on the same page.
4. Train Employees on Information Sharing
Provide training sessions that emphasize the importance of data sharing and collaboration. Equip your employees with best practices to ensure they understand how to leverage shared resources effectively.
5. Regularly Review and Update Processes
Set up feedback loops to continuously assess information sharing practices and amend them as necessary. An ongoing commitment to improving these channels can reduce the risks associated with information silos.
Real-World Examples of Overcoming Information Silos
To further illustrate the potential for conquering information silos problems, let’s examine some organizations that have successfully navigated these challenges:
Case Study: John Deere
John Deere, a leader in agricultural machinery, faced significant issues stemming from information silos. By transitioning to a shared digital platform, they not only improved internal communications but also enhanced their customer service. This transformation resulted in quicker turnaround times on machinery repairs, which bolstered customer satisfaction and loyalty.
Case Study: AGCO Corporation
AGCO Corporation recognized the inefficiencies caused by departmental silos in their service delivery. They implemented integrated software solutions that allowed data transparency across departments. This initiative facilitated better inventory management and streamlined the repair processes, leading to improvements in service quality.
Conclusion: The Path Forward
Addressing information silos problems is not merely a task; it's a strategic imperative for any farming equipment repair business aiming to thrive in today's competitive environment. By fostering communication, investing in collaborative technologies, and facilitating a culture of open data sharing, businesses can enhance efficiency and customer satisfaction.
We encourage all businesses, particularly those within the farm equipment sector like TSGC Inc., to assess their current processes and consider the implementation of the strategies discussed. Embracing change for better information flow can enhance service quality, reduce inefficiencies, and unlock new opportunities for growth.
Call to Action
If you're ready to tackle information silos problems head-on, reach out to us at TSGC Inc. today. Let’s work together to enhance your operational efficiency and take your farming equipment repair business to the next level!